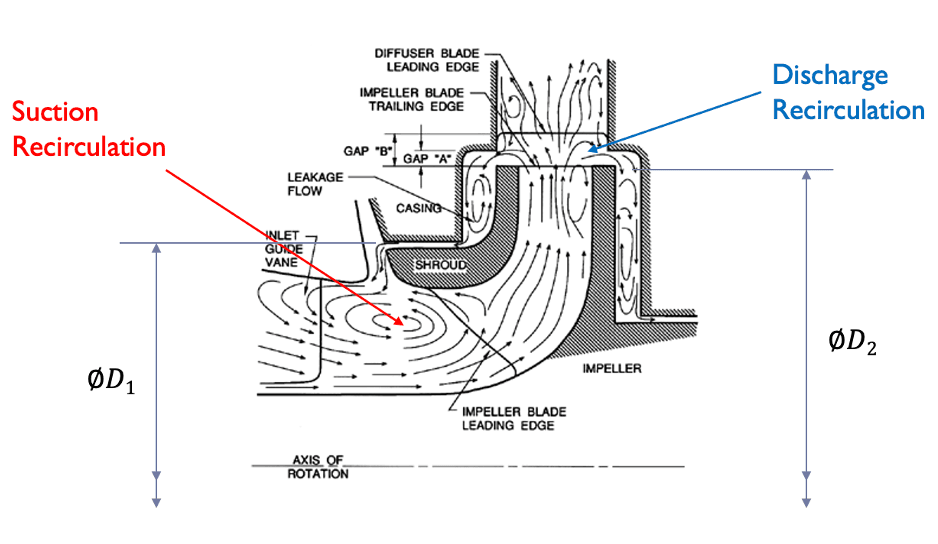
Troubleshooting Centrifugal Pumps: A Comprehensive Guide
Troubleshooting Centrifugal Pumps: A Comprehensive Guide
Centrifugal pumps are critical components in many industrial processes. This guide provides a methodical approach to troubleshooting recurring pump failures, helping to minimize downtime and optimize performance.
Introduction
Bearings and seals are often the first components to fail in a pump, acting as "fuses" and signaling underlying issues. However, shaft breakage and motor burnout can also occur. It's crucial to differentiate between root causes and their effects, as pump failures may result from various external factors.
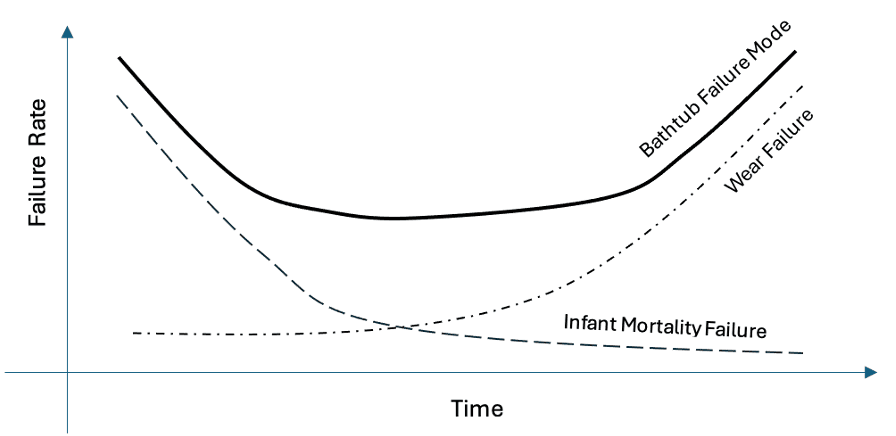
Expected Pump Lifespan
Generally, pumps are designed for at least two years of uninterrupted service, with a minimum service life of 20,000 hours for bearings, mechanical seals, and motors. Failures within the first few weeks or months of operation are abnormal and require immediate attention.
Troubleshooting Methodology
A methodical approach to troubleshooting includes:
-
Hydraulic Review: Confirm that the pump meets the current duty at the expected power, has a healthy NPSH margin, and operates in a stable region of its curve.
-
Mechanical Audit: Check the integrity of the construction, material selection, and rotordynamic stability of the machine.
-
Process Audit: Verify the heat and mass balance, operational philosophy, pressure drops in the system, and required pump duty.
-
Operational Review: Identify key time stamps and operational changes coinciding with failures.
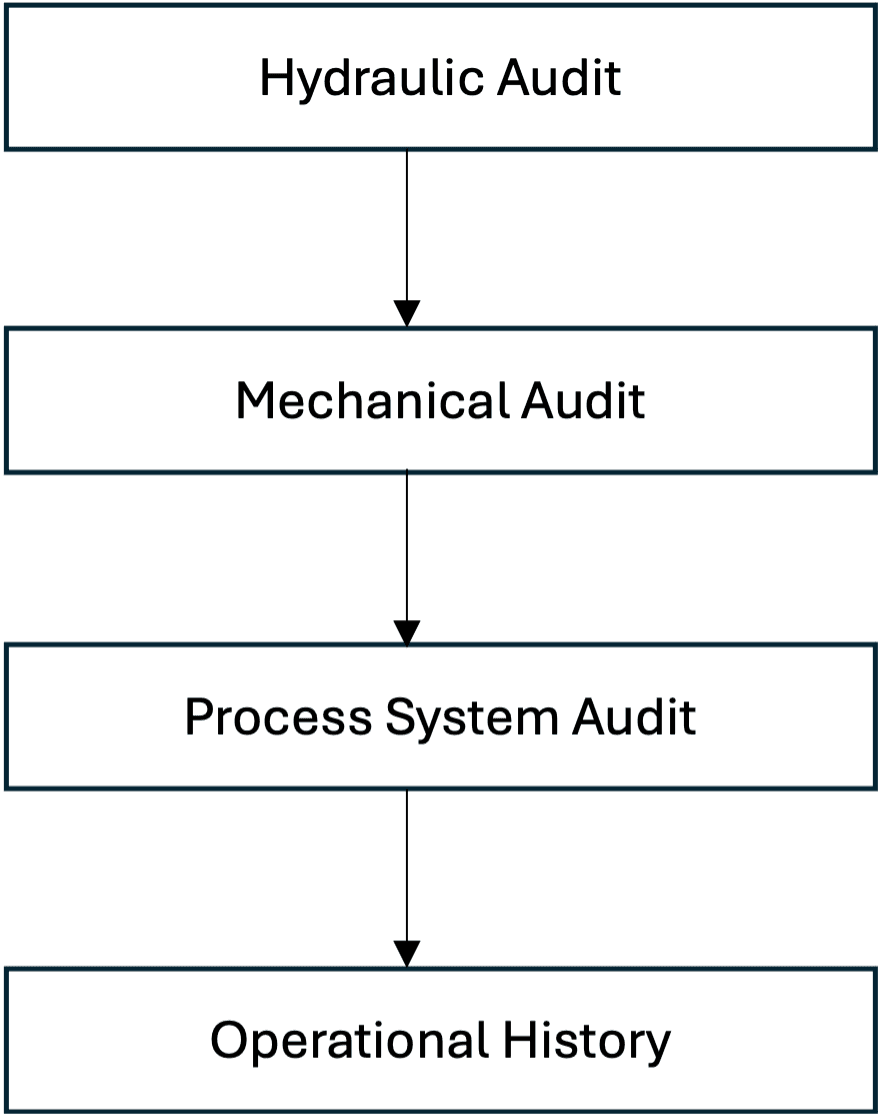
Common Checks for Problematic Pumps
- Off-Design Operation: Ensure the pump operates above its Minimum Continuous Stable Flow (MCSF) and preferably within its Preferred Operating Range (POR).
- Priming: Check for proper priming and air leaks in the suction line.
- Impeller: Inspect for damage, blockages, or corrosion.
- Speed: Verify correct operating speed.
- Alignment: Ensure proper alignment with the driver.
- Bearings / Seals: Inspect and replace if worn or damaged.
- Blockage: Check for blockages in the pump, suction strainer, recirculation port, valve, or discharge line.
- NPSH Margin: Recalculate based on actual site data.
- Electrical connections: Verify correct voltage and continuity.
- Control devices: Ensure proper operation of pressure switches and starters.
- Suction limit: Don't exceed a suction height of 18 feet for centrifugal pumps.
- Vortex Flow: Check for vortex flow in the intake or sump.
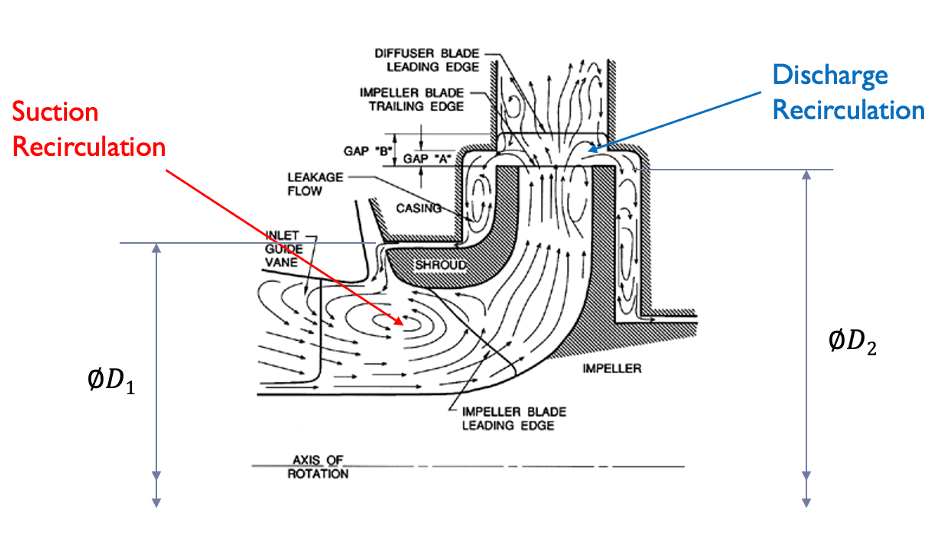
Most systems are a combination of both friction and static head. Understanding your specific system characteristics is crucial for effective troubleshooting and optimization.
Why This Matters
Effective troubleshooting of centrifugal pumps is crucial for:
- Minimizing downtime and production losses
- Extending equipment lifespan
- Optimizing energy efficiency
- Reducing maintenance costs
- Ensuring process reliability and safety
Did You Know?
- Improper pump selection accounts for nearly 20% of all pump failures.
- Up to 90% of pump failures can be prevented through proper installation, operation, and maintenance practices.
- Energy costs typically account for 40% of the total life cycle cost of a pump system.
Further Reading
For more in-depth information on centrifugal pump troubleshooting and maintenance, consider exploring these resources:
- Hydraulic Institute - Pump Systems Matter
- U.S. Department of Energy - Improving Pumping System Performance
Contact
For more information and support, please contact:
Dr Jean-Noel Bajeet FIMechE CEng
Lead Consultant
Jean-noel.bajeet@fluensys.co.uk
While every effort has been made to provide a comprehensive overview of best practices in troubleshooting pumps, Fluensys does not claim that these will successfully apply to every system and reserves the right to adjust their technical opinion to reflect latest practices and specifics of application.
Download Full Article
Get a PDF version of this article for offline reading and sharing.
Related Articles in [ troubleshooting ]
Subscribe to Our Blog
Stay updated with our latest articles and insights.